複合硬化処理
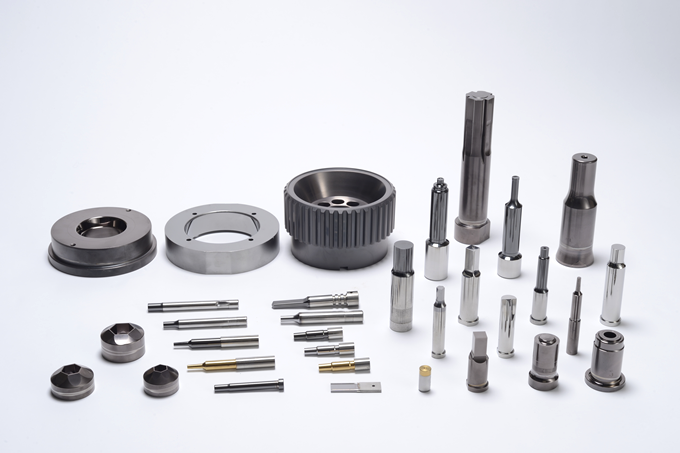
製品の特徴
対象製品
シャンクツール | チップ | ホブ・ピニオン | 丸刃 | 機械部品 |
△ | △ | × | × | ◎ |
プレス金型 | 樹脂金型 | 粉末成形金型 | ダイカスト金型 | その他 |
◎ | ○ | ◎ | ◎ | ○ |
PVD(物理蒸着法)法が高機能表面処理として切削工具、金型等の様々な分野で用いられ、TiN(窒化チタン)をはじめとして、TiCN、TiAlN等の被膜を提供して参りました。
しかし、昨今の表面処理に対するニーズはより高性能化・低コスト化が要求され、より厳しい使用条件に耐えうる表面処理が求められるようになって参りました。
今回ご紹介する新しい複合処理技術は従来からある熱処理技術と蒸着法を組み合わせ、それぞれの処理の相乗効果を狙うものです。
複合処理は、上図のように主に窒化、浸炭といった拡散硬化法を利用して、コーティングの基材に傾斜化された効果領域を形成し、機械的強度を向上させ、被膜の持つ特性と相乗効果を生み出すものです。
特に窒化処理では、表面粗度の変化が少なく、拡散層のみを形成することのできる「ラジカル窒化」を適用することにより、一層効果的な複合処理を開発いたしました。以下に金型へ適用した事例をご紹介します。
また窒化処理後、拡散層を形成することのできないオーステナイト系の鋼に対して、「IP窒化」を適用することにより、一層効果的な複合処理を開発いたしました。以下に機械部品へ適用した事例をご紹介します。
SUS304機械部品への適用例
これまで、定期的にTiNコーティングが必要であった部品が、下地の補強効果でメンテナンスフリーとなりました。
複合処理は、現在お使いのコーティング膜と組み合わせることで、一層の耐久寿命の向上が図れます。
処理の組合せについてはお気軽にご相談ください。
冷間鍛造試験結果
観察結果および考察
上の写真は、図1に示します冷間鍛造を100ショット行った後に直径15mmのポンチ先端R部分を観察した結果です。未処理では、ポンチ先端は、直径20mmの被加工材にかじりつきを発生しました。これは、SKH51の炭化物がマトリックスとの硬度差が大きいために脱落したことによります。
PVD-VCでは、皮膜に分散しているVCがプレスによって欠落して縦方向に深いキズを形成しているのが判ります。これに対して下地のSKH51の硬度差による変形の影響を受けにくい複合硬化処理では、キズが見られません。
試験条件
・160tナックルジョイントプレス
(神奈川県産業技術センター)
・ポンチ材質:SKH51(63HRC)+各種表面処理
・被加工材:SS400(ボンデ処理)
キズ深さ測定結果
各種表面処理 | |
複合硬化処理 | 膜厚3.0μm;2200HV0.025 |
PVD-VC | 膜厚3.3μm;2400HV0.025 |
PVD-CrN | 膜厚3.0μm;2000HV0.025 |
CVD-TiC/N | 膜厚8.0μm;2200HV0.025 |
TD-VC | 膜厚10.0μm;3300HV0.025 |
上の図は、図1の冷間鍛造を100ショット行った後に直径15mmのポンチ先端平面部分を超深度形状測定顕微鏡(レーザ顕微鏡)で測定した最大キズ深さの結果です。
どこか1箇所でも大きなキズが発生すると、そこがかじりつきの原因となることから、この数値が各種表面処理の寿命の指標となります。複合硬化処理では、膜厚10μmのTD-VCに匹敵する小さなキズ深さとなり、大きなアドバンテージが得られます。
測定に使用した機器:超深度形状測定顕微鏡
断面硬度分布
各処理時間でラジカル窒化処理されたSKH51の断面硬度曲線(処理条件:500℃)
断面組織
窒化後の断面組織写真
(基材:SKH51、エッチング:ナイタル)
化合物層はありません
処理温度500℃
適用材料例
合金工具鋼 | SKD61 | プリハードン鋼 | HPM1, HPM50 |
SKD11(高温戻し) | NAK55, NAK80 | ||
高速度工具鋼 | SKH51, SKH57, HAP50 | 構造用合金鋼 | SACM645, (SCM) |
ラジカル窒化と他の窒化法による表面祖度の変化と窒化状態
鋼種 | 処理法 | 表面硬度 | 化合物層 | 拡散層 | 表面粗度 | 表面粗度 |
HV0.1 | μm | μm | Ra | Rmax | ||
SKD61 | 未処理 | 592 | - | - | 0.02 | 0.05 |
ラジカル窒化 | 1230 | 0 | 130 | 0.04 | 0.2 | |
ガス軟窒化 | 894 | 12 | 130 | 0.18 | 2.88 | |
イオン窒化 | 1250 | 8 | 100 | 0.14 | 0.98 |
ラジカル窒化と複合硬化処理の応用例と効果
ラジカル窒化を用いると、射出成形、プレス成形等で使用される金型、各種部品の寿命が著しく延びます。特にプリハードン鋼使用の金型では、寸法変化がないため最適です。当社では金型以外にも治具などの各種機械部品へのラジカル窒化処理の適用を進めております。
種類 | 処理 | 効果 | |
樹脂型 | キャビティ | 窒化 | ・窒化後の研磨不要 |
コア、ピン | ・型寿命:約5倍(未処理品と比較) | ||
プレス型 | 粉体(フェライト) | 窒化 | ・型寿命:2~5倍 |
鍛造型(鋼塊) | 窒化+TiCN, CrN | ・耐面圧性向上 | |
絞り型(鋼板) | ・膜剥離発生が大幅減少 | ||
曲げ型(鋼板) | ・型寿命:2~3倍(成膜処理品と比較) | ||
成形ロール | 転造 | 窒化+TiCN | ・CVD処理品より熱変形小 |
フォーミング | ・ダイス寿命:2~3倍(成膜処理品と比較) | ||
バニシング | |||
射出成型機関連 | スクリュー | 窒化 | ・窒化後の研磨が不要 |
バレルなど | ・寸法精度向上 | ||
押し出し機関連 | ゴム押し出しダイス | 窒化 | ・型寿命:約10倍(未処理品と比較) |
機械部品 (合金工具鋼) |
耐摩耗治具 | 窒化+TiN, TiCN, CrN | ・寿命:2~5倍(成膜処理品と比較) |
機械部品 |
ラジカル窒化処理のメリット
硬度低下、歪みがない
500℃以下の温度で処理。よって、SKD,SKH等であれば、残留応力が無ければ硬度低下、歪みは発生しない。
処理後の磨きが不要
イオン窒化、ガス窒化は表面に化合物層ができ方面が荒れるため、処理後バフ磨きが必要である。本処理は化合物層が出来ず、表面の面荒れがないため、バフ磨きが不要。
剥離がない
窒化は表面皮膜処理と異なり、拡散浸透型のため膜の剥離がない。
複合処理が可能
イオン窒化の場合、表面の化合物層を完全に取り除く必要があったが、本処理はそのままコーティング可能。
窒化深さが均一
従来、イオン窒化の場合、先端部分やコーナー部が重点的に窒化される傾向があったが、本処理の場合均一である。